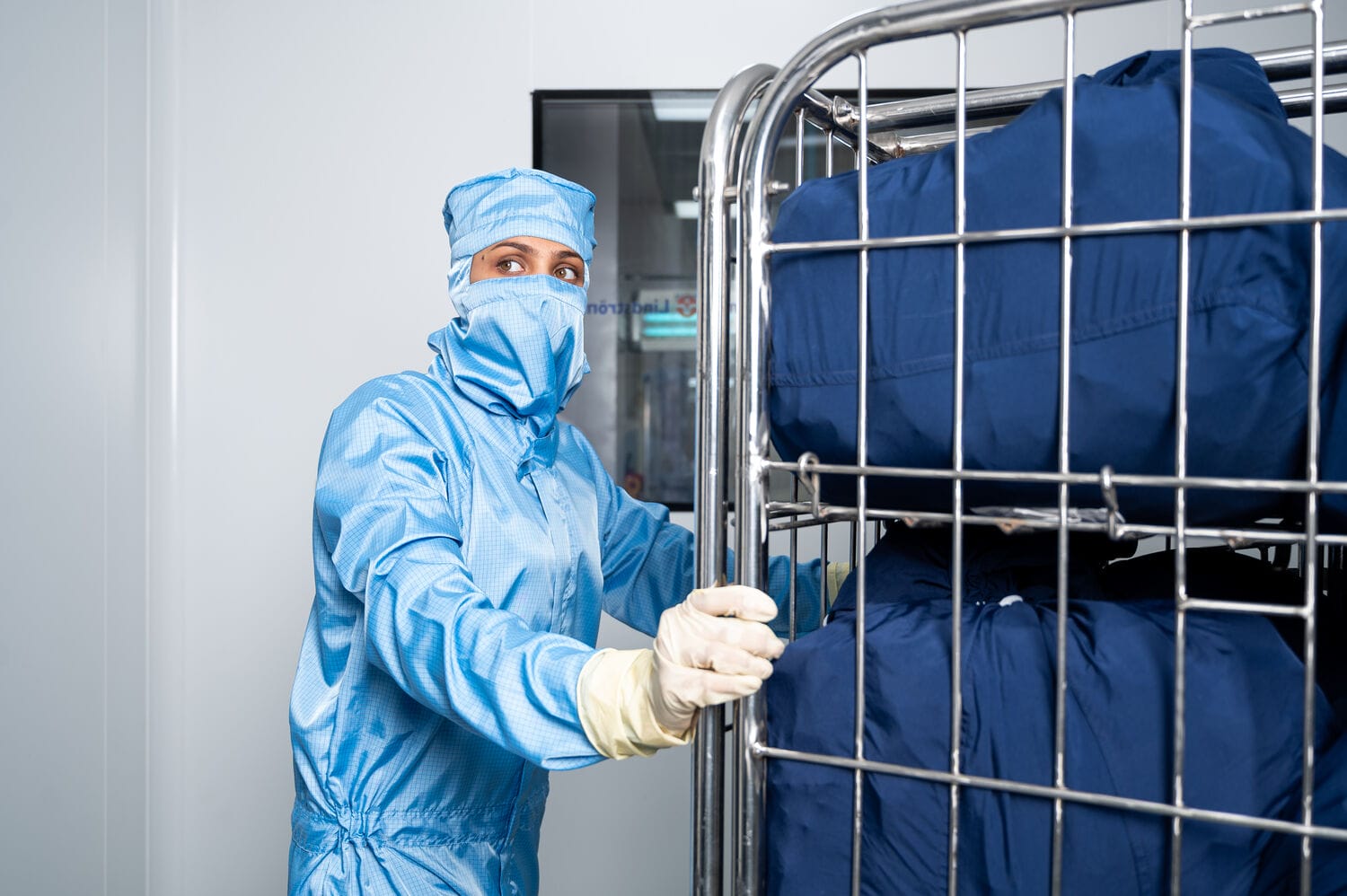
Guide to ISO Class 7 cleanroom cleaning procedures
An ISO Class 7 cleanroom is a controlled environment that maintains strict cleanliness levels to prevent contamination in sensitive manufacturing processes. According to ISO 14644-1, a Class 7 cleanroom must not exceed 352,000 particles per cubic meter (≥0.5 microns). Compliance with these standards ensures that industries such as pharmaceuticals, electronics, and aerospace maintain product integrity and meet regulatory requirements.
Beyond particle count limitations, cleanrooms must adhere to Good Manufacturing Practice (GMP) Annex 1, ensuring control over air changes per hour (ACPH), filtration efficiency, and pressure differentials between classified areas. These cleanrooms are equipped with HEPA filters, smooth surfaces to minimize particle accumulation, and strict gowning protocols to reduce contamination risks.
The importance of proper cleaning procedures
Maintaining rigorous cleaning procedures in an ISO Class 7 cleanroom is essential to ensure compliance and prevent contamination. Improper cleaning can lead to microbial growth, cross-contamination, and costly product recalls. In regulated industries like pharmaceuticals, contamination can directly impact patient safety and result in regulatory non-compliance.
Failing to adhere to cleaning standards poses significant risks, including:
- Product contamination and batch rejection
- Increased regulatory non-compliance risks
- Microbial excursions requiring costly remediation
- Potential reputational damage due to failed audits
A structured cleaning protocol is essential to mitigate these risks and maintain a controlled environment.
Essential tools and materials for cleanroom cleaning
To maintain compliance with ISO Class 7 standards, specialized cleaning tools and materials are required. These include:
Tool/Material | Purpose |
---|---|
Non-shedding mops & wipes | Prevents introduction of foreign particles |
Sterile water & isopropyl alcohol (IPA) | Disinfection of surfaces |
HEPA-filtered vacuum systems | Removes fine particles |
Disposable or autoclave-safe cleaning cloths | Ensures sterility in cleaning practices |
Pre-validated disinfectants | Complies with ISO 14644 & GMP Annex 1 |
Using incorrect materials, such as shedding cloths or unvalidated chemicals, can introduce contaminants rather than eliminate them, making it essential to select the right cleaning agents and tools for the cleanroom environment.
Step-by-step cleaning procedures
Cleaning an ISO Class 7 cleanroom follows a structured approach to maintain hygiene and regulatory compliance.
Pre-cleaning preparation
Before cleaning begins, personnel must wear ISO-compliant cleanroom garments, including coveralls, gloves, shoe covers, hoods, and goggles. Cleaning solutions and tools should be gathered in advance, and large debris should be removed using a HEPA-filtered vacuum.
Cleaning sequence (Top-to-bottom approach)
The cleaning process should always follow a top-to-bottom method, ensuring that airborne particles are effectively removed.
Area | Cleaning Method |
Ceilings & walls | Wipe with sterile, low-lint mop & IPA |
Work surfaces & equipment | Wipe with sterile disinfectant |
Floors | Mop with non-shedding mop & sterile disinfectant |
High-touch areas (door handles, switches) | Clean with IPA wipes |
Post-cleaning validation
After cleaning, a thorough inspection is conducted to check for residues or streaks. Environmental monitoring, including particle count and surface bioburden testing, is performed to confirm compliance. Cleaning logs should be documented as per GMP and ISO 14644 standards.
Common challenges and solutions in cleanroom cleaning
Challenge | Solution |
Inconsistent cleaning by staff | Implement regular training & audits |
Cross-contamination from personnel | Enforce strict gowning & entry protocols |
Equipment malfunction leading to contamination | Schedule routine equipment maintenance |
Improper cleaning technique | Use validated cleaning protocols & checklists |
Regular quality audits and personnel training ensure that protocols are consistently followed, reducing contamination risks.
Training and certification for cleanroom personnel
Advancements in technology are helping improve the efficiency of cleanroom cleaning processes. Some key innovations include:
- Automated robotic cleaners reduce human contact with surfaces.
- RFID tracking for garments and equipment ensures compliance with lifecycle management.
- Airborne particle monitoring sensors provide real-time contamination detection, enabling proactive interventions to maintain cleanliness standards.
Leveraging these advanced technologies minimizes contamination risks and enhances regulatory compliance, making cleanroom management more effective and reliable.
The role of technology in better cleaning processes
Modern technology plays a significant role in enhancing the efficiency of cleaning processes in ISO Class 7 cleanrooms. Automated cleaning systems, such as robotic vacuum cleaners and mopping robots, can reduce the time and effort required to maintain cleanliness. These systems are designed to operate with minimal human intervention, reducing the risk of contamination from personnel.
Advanced monitoring technologies, including sensors and data analytics, provide real-time insights into the cleanroom’s conditions. These tools enable proactive interventions, allowing for adjustments to cleaning schedules and methods based on actual contamination levels. By leveraging technology, cleanroom operators can achieve a higher standard of cleanliness while optimising resource use and minimising downtime.
Ensure hygiene, safety & compliance of garments with Lindström’s cleanroom service
Maintaining an ISO Class 7 cleanroom requires more than just cleaning—it demands validated garments, controlled laundering, and traceable contamination control measures. Lindström’s cleanroom rental services provide:
- GMP-compliant garments with RFID tracking for traceability
- Validated laundering processes in ISO-classified facilities
- Sustainable textile solutions reducing waste and environmental impact
Outsource your cleanroom garment management to Lindström today and ensure continuous compliance with industry standards.
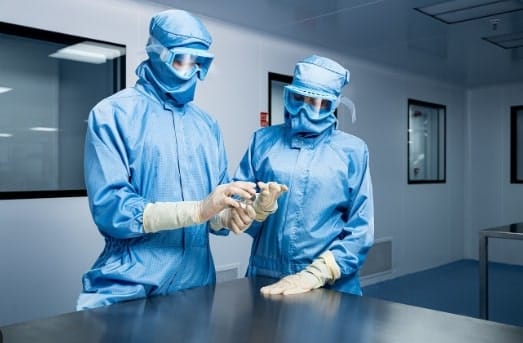