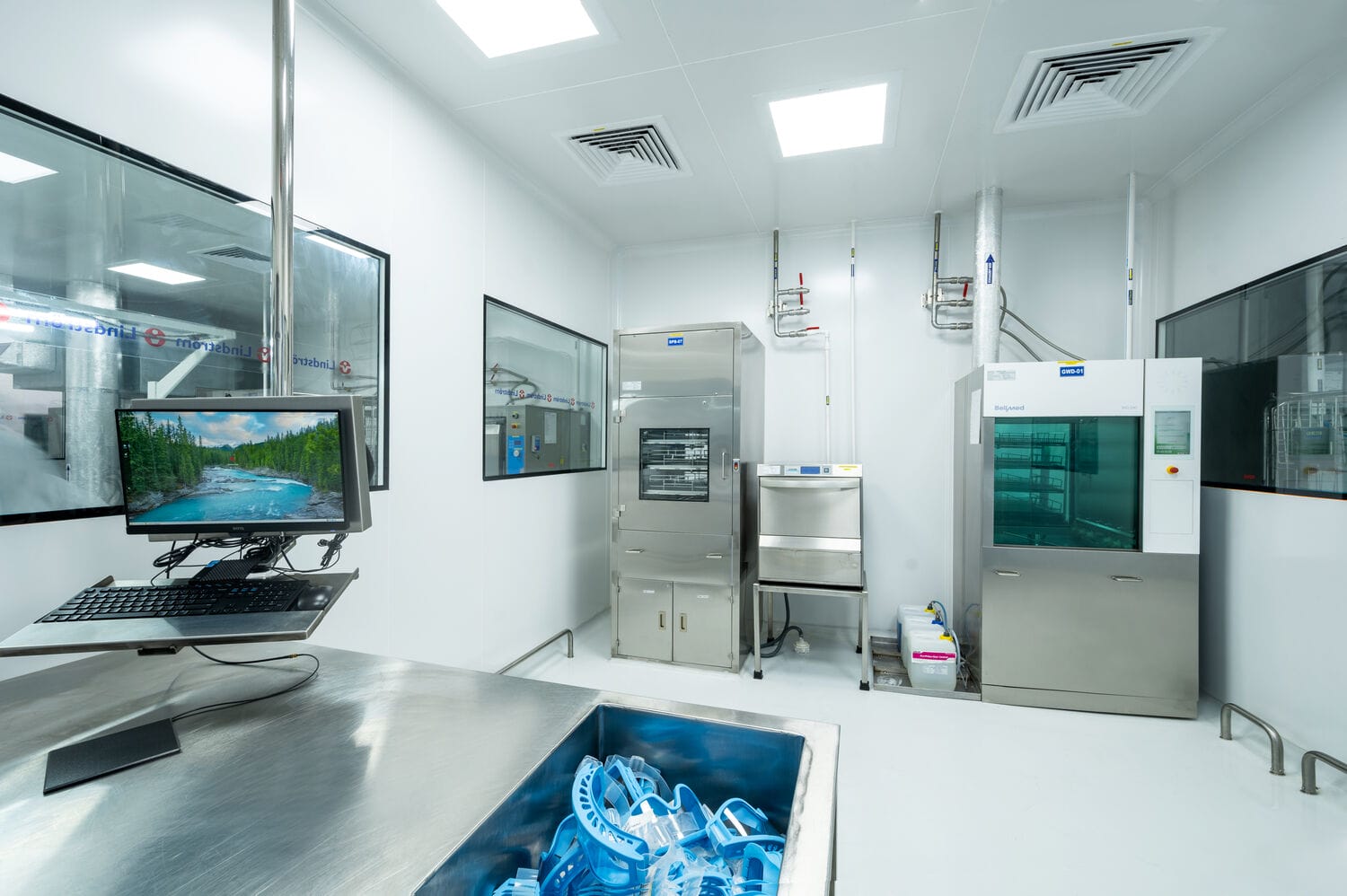
ISO Class 8 cleanroom gowning procedure: best practices
Maintaining contamination control in an ISO Class 8 cleanroom is essential for ensuring product integrity, process reliability, and regulatory compliance. Cleanrooms are controlled environments where airborne particles, dust, and microbes are minimized to prevent contamination. ISO 8 classification permits up to 3,520,000 particles (≥0.5µm) per cubic meter of air, making it one of the less stringent cleanroom classifications, yet still requiring strict gowning protocols to prevent contamination.
Gowning procedures serve as a primary defense against contamination risks, particularly in industries such as pharmaceuticals, biotechnology, and electronics, where even minor particulates can compromise product safety and yield. By following best practices in gowning, companies can enhance operational efficiency while adhering to international standards like ISO 14644 and Good Manufacturing Practices (GMP).
Principles of the ISO 8 gowning procedure
Effective gowning for an ISO 8 cleanroom follows a structured process designed to minimize contamination transfer. The standard protocol involves entering a designated gowning area and donning cleanroom attire in a specific order. Personnel must wash and dry their hands thoroughly before gowning. They first put on a bouffant cap or hood to contain hair, followed by a face mask to reduce the spread of respiratory droplets. Shoe covers are then worn before stepping onto a sticky mat or into a gowning area.
Once these initial garments are secured, personnel don a cleanroom coat, frock, or coverall, depending on industry requirements. If required, non-sterile but clean gloves are worn to avoid skin particle transfer. The final step involves ensuring all garments fit securely, with no exposed skin or loose fibres that could become contamination sources.
Key considerations for gowning:
- Hygiene discipline: Proper handwashing and adherence to protocol reduce contamination risks.
- Garment integrity: Regular checks ensure garments are free from damage and deterioration.
- Correct sequencing: Following the right order minimizes particle transfer to clean areas.
ISO 8 gowning procedures are generally less restrictive than those in ISO 7 or ISO 5 cleanrooms, where sterile gloves, hoods, and full-body coveralls are typically mandatory. However, adherence to proper sequencing and hygiene remains critical to minimizing contamination risks.
Practical applications of ISO Class 8 gowning procedures
ISO Class 8 gowning procedures find practical applications in various industries where contamination control is paramount. In the pharmaceutical sector, for instance, maintaining sterility is critical during the manufacturing of drugs and vaccines. Here, gowning protocols ensure that personnel do not introduce contaminants that could compromise product safety and efficacy.
In the electronics industry, cleanrooms are used during the fabrication of semiconductors and other sensitive components. The meticulous gowning procedures help prevent dust and other particles from affecting the production process, thereby reducing defects and improving yield. By adhering to ISO 8 gowning requirements, companies can enhance operational efficiency and product quality.
Innovations in cleanroom gowning
Recent advancements in cleanroom gowning are enhancing both contamination control and wearer comfort. Modern cleanroom garments now feature electrostatically dissipative (ESD) properties and antimicrobial coatings, reducing particulate shedding and bacterial growth. The shift toward reusable ISO-certified garments is gaining momentum, cutting down on waste while ensuring compliance through validated laundering cycles.
Additionally, automation is improving gowning efficiency, with RFID-tracked garments and automated dispensers helping personnel gown more effectively while maintaining traceability. Innovations in fabric engineering have led to lightweight, breathable materials that improve wearer comfort without compromising protection. These innovations contribute to both compliance and operational efficiency, ensuring that cleanroom environments remain protected without adding unnecessary burdens on personnel.
Key Innovations:
Automated tracking systems: RFID solutions improve traceability and accountability.
Advanced fabric technology: ESD-safe, antimicrobial coatings for enhanced protection.
Sustainability-focused reusables: Reduces waste while maintaining compliance.
Challenges in maintaining gowning discipline
Despite well-defined protocols, maintaining strict gowning discipline can be challenging due to various factors. Human error is a common issue, as incorrect donning and doffing techniques can introduce contamination. Non-compliance is another concern, as personnel may deviate from procedures due to time constraints or lack of awareness. Additionally, repeated laundering cycles can degrade garment integrity, leading to increased particulate release.
To address these challenges, comprehensive training programs should be implemented to educate personnel on proper gowning techniques and contamination risks. Routine gowning audits and real-time compliance tracking using RFID technology can help monitor adherence to procedures. Establishing clear guidelines on the maximum number of wash cycles for each garment ensures they remain effective over time.
ISO 8 gowning compared to other cleanroom standards
ISO 8 cleanroom requirements differ from those of stricter cleanroom classifications such as ISO 7 or ISO 5. Particle count limits in ISO 8 are higher than in ISO 7 and ISO 5, requiring less stringent controls. The complexity of gowning also varies.
- ISO 8: Requires frocks, face masks, shoe covers, and hair coverings.
- ISO 7: Necessitates full coveralls, gloves, and boots.
- ISO 5 and below: Demands sterile gloves, face coverings, and full-body suits to minimize microbial risks.
Understanding these differences helps companies ensure they adopt appropriate gowning procedures based on their specific cleanroom classification needs.
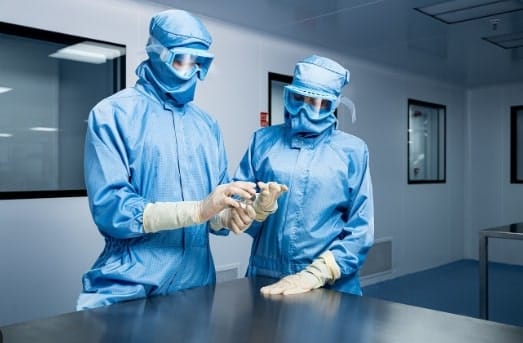