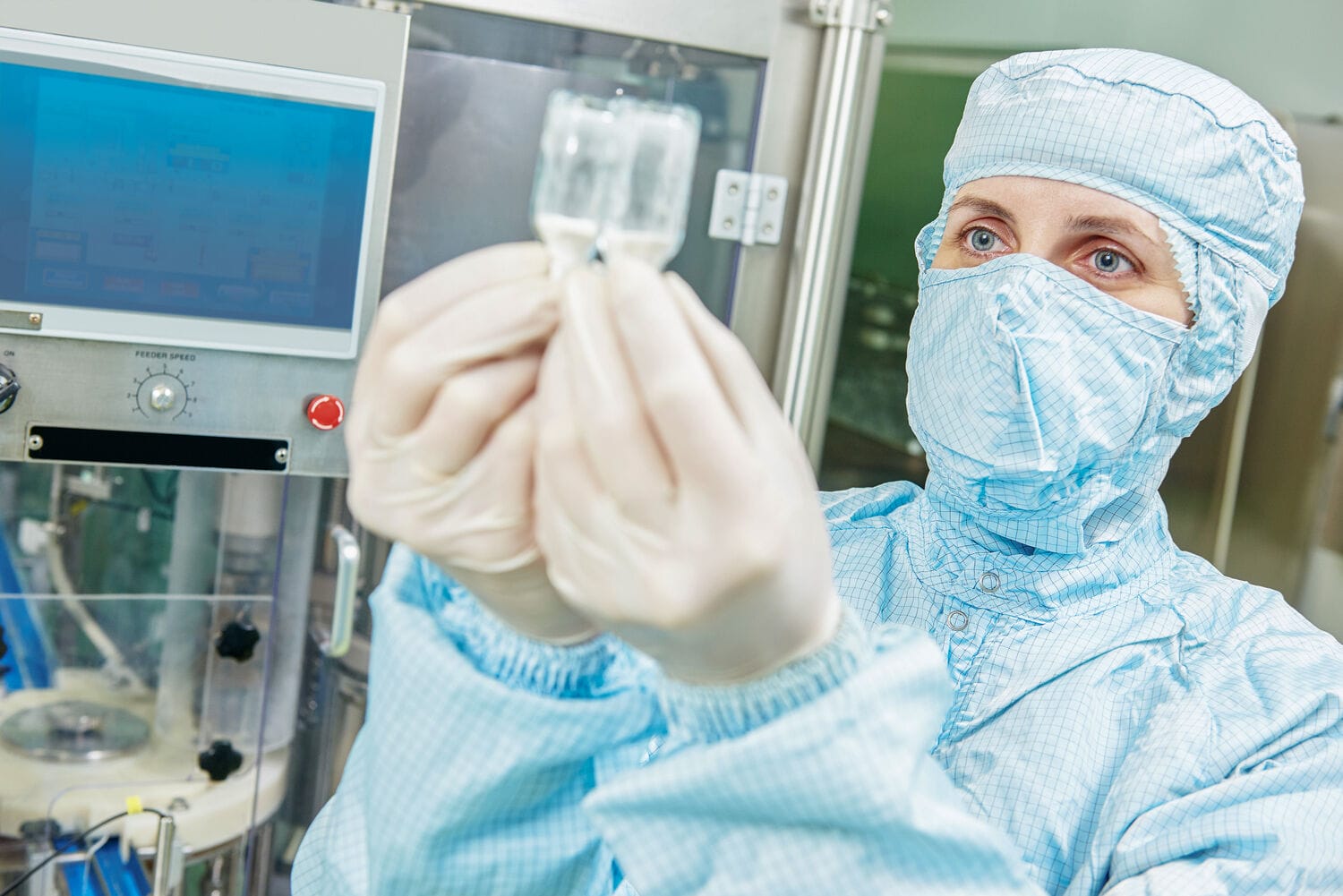
ISO Class 7 vs ISO Class 8 Cleanroom Garments
In cleanroom environments, ISO Class 7 garments help maintain strict contamination control, especially in industries like pharmaceuticals, where every particle counts. Guided by ISO 14644-1, this classification ensures that cleanrooms maintain the highest standards of cleanliness. ISO Class 7 apparel is specifically designed to filter out contaminants using tightly woven materials, advanced particle filtration techniques, and electrostatic properties that help trap and control particulates, ensuring the highest level of cleanliness for controlled environments. These garments are critical in industries where maintaining strict cleanliness is needed, such as pharmaceuticals, biotechnology, and electronics.
- Limits particles to 352,000 per cubic meter (0.5 microns and larger)
- Commonly used in pharmaceuticals, biotechnology, and electronics
- Includes coveralls, hoods, masks, gloves, and boots
- Materials resist particle shedding and microbial penetration
- Tested using Helmke Drum and particle filtration tests
Understanding ISO Class 8 garments:
ISO Class 8 garments cater to environments where contamination control requirements are less stringent than those of ISO Class 7. With a higher particle allowance, ISO Class 8 cleanrooms are designed with practicality and efficiency in mind, making them suitable for various industrial applications. ISO Class 8 apparel is ideal for industries with less stringent contamination control requirements, such as automotive manufacturing and food processing.
- Allows up to 3,520,000 particles per cubic meter (0.5 microns and larger)
- Used in automotive manufacturing, food processing, and some electronics
- Similar garments to ISO Class 7 but with less rigorous materials
- Focuses on protecting less sensitive processes from contamination
- May undergo fewer rigorous tests depending on the application
Key Differences Between ISO Class 7 and ISO Class 8 Clothing:
The primary differences between ISO Class 7 and ISO Class 8 clothing lie in particle filtration efficiency and material construction. ISO Class 7 clothing utilizes advanced fabrics for superior filtration, accommodating stricter particle control requirements, while ISO Class 8 apparel balances effectiveness with practicality. Understanding these differences is crucial for industries to select the appropriate cleanroom attire based on their specific contamination control needs.
Aspect | ISO Class 7 | ISO Class 8 |
---|---|---|
Particle Limit | 352,000 particles/m³ | 3,520,000 particles/m³ |
Material Technology | Advanced, tightly woven | Less advanced |
Cost and Durability | Higher | Moderate |
Design Complexity | Comprehensive with tighter seals | Simpler design |
Practical applications of ISO Class 7 and 8 garments:
The choice between ISO Class 7 and ISO Class 8 garments is determined by the contamination control needs of specific industries. High-stakes fields like pharmaceuticals and biotechnology demand the stringent controls of ISO Class 7 apparel, whereas industries with less sensitivity to particles, such as automotive and food processing, often opt for ISO Class 8 solutions. Adopting the right ISO class clothing ensures product integrity and minimizes contamination risks.
- ISO Class 7: Pharmaceuticals, biotechnology
- ISO Class 8: Automotive manufacturing, food processing
Non-compliance can lead to severe consequences such as contamination, product recalls, and regulatory penalties, impacting business reputation and finances.
Challenges in choosing the right ISO class clothing:
Choosing the appropriate ISO class clothing involves balancing protection levels with cost considerations. While ISO Class 7 offers higher protection with advanced materials, it also comes at a higher price point. Industries must evaluate their specific needs to make informed decisions, ensuring compliance without compromising worker comfort and usability. By understanding the operational and regulatory demands, companies can make strategic choices in cleanroom apparel.
- Assess cleanroom operational needs
- Consider regulatory requirements and material sensitivity
- Consult with experts for optimal solutions
Selecting the right ISO class clothing involves navigating operational, regulatory, and sustainability challenges. At Lindström, we simplify this process by offering end-to-end cleanroom solutions that balance protection, compliance, and cost-efficiency. Solutions like Lindström cleanroom services can assist you in navigating these challenges, and ensure both compliance and efficiency.

Frequently Asked Questions (FAQ)
The primary difference lies in particle control requirements. ISO Class 7 cleanrooms permit up to 352,000 particles per cubic meter (≥0.5 microns), necessitating garments made from advanced, tightly woven fabrics with comprehensive designs to ensure superior filtration. Conversely, ISO Class 8 cleanrooms allow up to 3,520,000 particles per cubic meter, so garments can be simpler in design and made from less advanced materials, balancing effectiveness with practicality.
Industries with stringent contamination control needs often require ISO Class 7 garments. Such industries have examples like pharmaceuticals, biotechnology, and medical device manufacturing. For the protection of sensitive processes as well as products, these environments do demand higher standards of cleanliness.
No, ISO Class 8 garments prove suitable for environments where contamination risks are lower. Automotive manufacturing, food processing, and certain electronics assembly areas exist as such environments. However, garments within ISO Class 7 are more appropriate for processes which require a stricter level of contamination control.
ISO Class 7 garments generally have higher costs due to their advanced materials and comprehensive designs required for stringent contamination control. ISO Class 8 garments, being less complex, are typically more cost-effective, making them suitable for industries where ultra-clean environments are not critical.
ISO Class 7 attire typically includes full-body coveralls, hoods, boots, gloves, and face masks, all designed to minimize particle shedding and maintain a controlled environment. The materials used are often non-linting and provide high filtration efficiency.
Using ISO Class 8 garments in ISO Class 7 cleanrooms is not recommended, as they may not meet the stricter particle control requirements. Employing garments that do not comply with the necessary standards can compromise the cleanroom’s integrity and lead to contamination risks.
Garment design plays a crucial role in maintaining cleanroom standards. Features like secure closures, minimal seams, and appropriate fit help prevent particle release. In ISO Class 7 environments, garments are designed with tighter seals and advanced materials to ensure higher levels of contamination control compared to those used in ISO Class 8 settings.