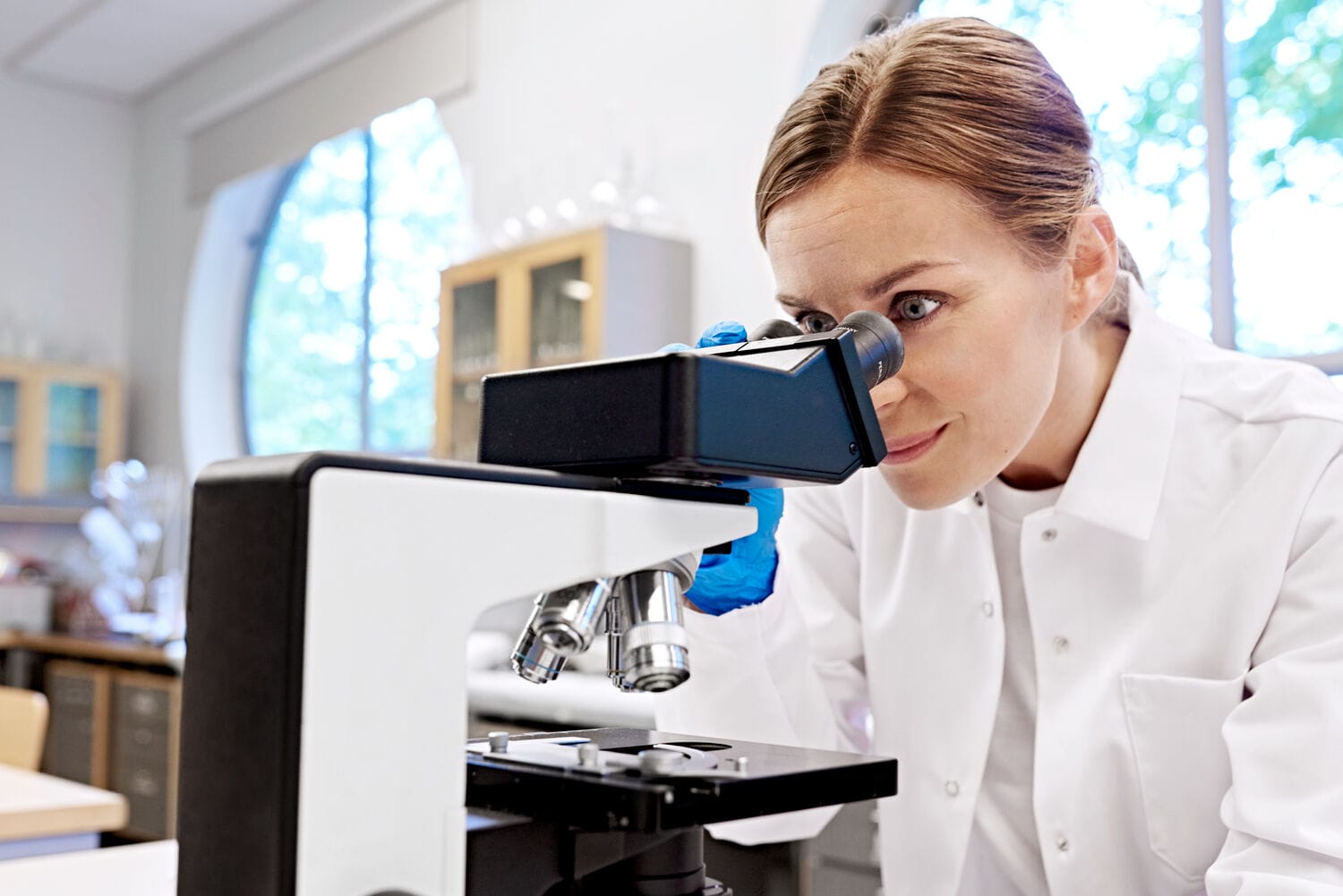
ESD smocks: better protection against static electricity
In manufacturing situations, especially in the electronic, pharmaceutical, and aeronautic industries, a phenomenon referred to as electrostatic discharge (ESD) becomes a matter of concern. Static electricity that is discharged from the human body can destroy delicate parts and pieces of equipment and render bands unfit for usage.
With development in these areas and evolving technology, the use of effective ESD protection workwear is increasingly becoming a requirement. For many years, ESD smocks and garments have been in sensible environments to keep control of the ESD phenomenon, and recent developments are taking the expansion of these protective wear even further.
ESD Apparel: Definition and Significance:
ESD garments are a special kind of clothing also known as ESD smocks, which are workwear developed to control static electric charges attracted to personnel and shielding static sensitive devices.
These types of garments are made of sweat-wicking clothes such as superfine polyester knits and are also made of conductive and dissipative fabrics, which help to conduct and dispel static electrical energy away from the individual’s body and thus govern any electrically charged bodies/ objects.
In measures where static electricity is very destructive, the wearer of ESD protection workwear is simply not a matter of taking extra precaution but rather an absolute requirement for all persons involved in electronics manufacturing or in semiconductor production. Even just a brief touch can create some static charge, which can damage fragile parts and lead to product defects, expensive repairs or even a standstill in the manufacturing process. By donning these anti-static garments, the employees assist in preventing this occurrence and preserving the quality of the sensitive electronic devices.
Recent Developments in ESD Garments and Smocks:
New trends regarding ESD garments have emerged in recent years as technology has improved. This is a response to the heightened need for ESD protection. Here are the latest developments you should know:
- More Efficient Conductive Fabrics: One of the remarkable advancements in ESD garments is the presence of clever conductive fibres incorporated in the garb. These fabrics have a better capacity to dissipate static charge compared to traditional materials and are built to last without degrading the ESD functionality even with prolonged use. Carbon or metallic fibres are used in the fabric to improve the conductivity of the material such that even before static charge builds up to a dangerous level, it is got rid of within no time.
- Light Weight and Comfortable wear: In addition to the intangible benefits, which have always been at the forefront, comfort is becoming more of a concern in ESD smock designs. In a modern manufacturing environment, employees may find themselves in ESD garments for hours on end. Because of this, there are now lighter and more comfortable fabrics that can be worn and still be ESD-safe. Such designs enable workers to be more productive as they can move around and be stress-free with ESD equipment.
- Environmentally Safe and Durable Elements: As climate change continues to be a dominant challenge in every sector, the clothing sector, particularly ESD garment industry is not left behind. Reuse and prolonging the useful life of products made in the ESD smock industry are emerging as effective strategies in helping companies mitigate environmental waste. Other manufacturers have also begun to use fewer controversial materials for reuse rather than other harmful methods of disposal.
- Antimicrobial ESD Garments: The other major trend is the addition of antimicrobial treatments to ESD garments. This is vital in some workplaces like pharmaceuticals or cleanrooms, which require as much control of contamination as static control. Antimicrobial ESD smocks prevent static discharge and help contain cleanness with a decreased risk of microbial contamination in critical areas.
- Personalization and Fit: Because workers can no longer tolerate discomfort and employers are coming around to the fact that endowed staff means happy models, personalized ESD garments are openly finding acceptance. All workers can wear appropriately fitting garments due to custom size options and the possibility of adjustable features, which ensures the comfort levels are rested so as not to affect their productivity. The better the fit of ESD smocks worn by employees, the more static hold-up capability is because if the clothing is too loose or ill-fitted, the microfabrics may not touch the skin enough to discharge the accumulated charges.
Conclusion:
There are few industries where the use of ESD garments, specifically the ESD smocks, in the question of control of any static discharges, especially regarding the sensitive electronics and components, is not paramount. As with all things, time brings in improvement in technology which in turn leads to changes in designs and materials of these garments for better functionality, comfort, and green features.
Because these trends can lead to the potential erosion of profit for the businesses, it is important that companies remain apprised of these latest trends in ESD protection workwear to devise ways and means of providing employees with workwear that is most efficient and effective.
Frequently Asked Questions (FAQ)
The demand for ESD garments grows in a rapid manner in aerospace, pharmaceuticals, advanced medical device manufacturing, electronics, and semiconductors. As products become smaller and more sensitive, even micro static charges pose risks—driving industries to adopt higher-performance ESD protection solutions.
Organizations often struggle with inconsistencies in fabric quality, lack of standardization, poor durability, and discomfort leading to non-compliance. Lindström addresses all these issues, as well as it ensures reliability and user comfort via tested certified garments that do meet international safety and ESD standards.
Lindström provides a full-service model including rental, professional laundering, RFID tracking, and quality inspection of ESD garments. This approach ensures continuous compliance, eliminates the burden of garment maintenance, and offers cost-effective scalability for businesses.
Even the best garments fail if not worn or grounded properly. Lindström emphasizes the need for routine staff training to ensure correct gowning techniques, grounding protocols, and understanding of garment care—minimizing the risk of human error in ESD-sensitive zones.
Yes, certifications such as ANSI/ESD S20.20 and IEC 61340-5-1 are global benchmarks for ESD compliance. Lindström ensures that its ESD workwear adheres to these standards, offering clients peace of mind during quality audits and compliance checks.
Innovations include embedded sensors to monitor static charge levels, moisture-wicking and breathable fabrics for comfort, and modular garments that can be adapted for dual protection (ESD and cleanroom). These features aim to merge high performance with user-centred design.
As mobile production units as well as flexible labs become more common, Lindström supports on-demand garment provisioning, compact storage solutions, and rapid replacement logistics—making ESD protection more accessible beyond static cleanrooms or dedicated manufacturing sites.