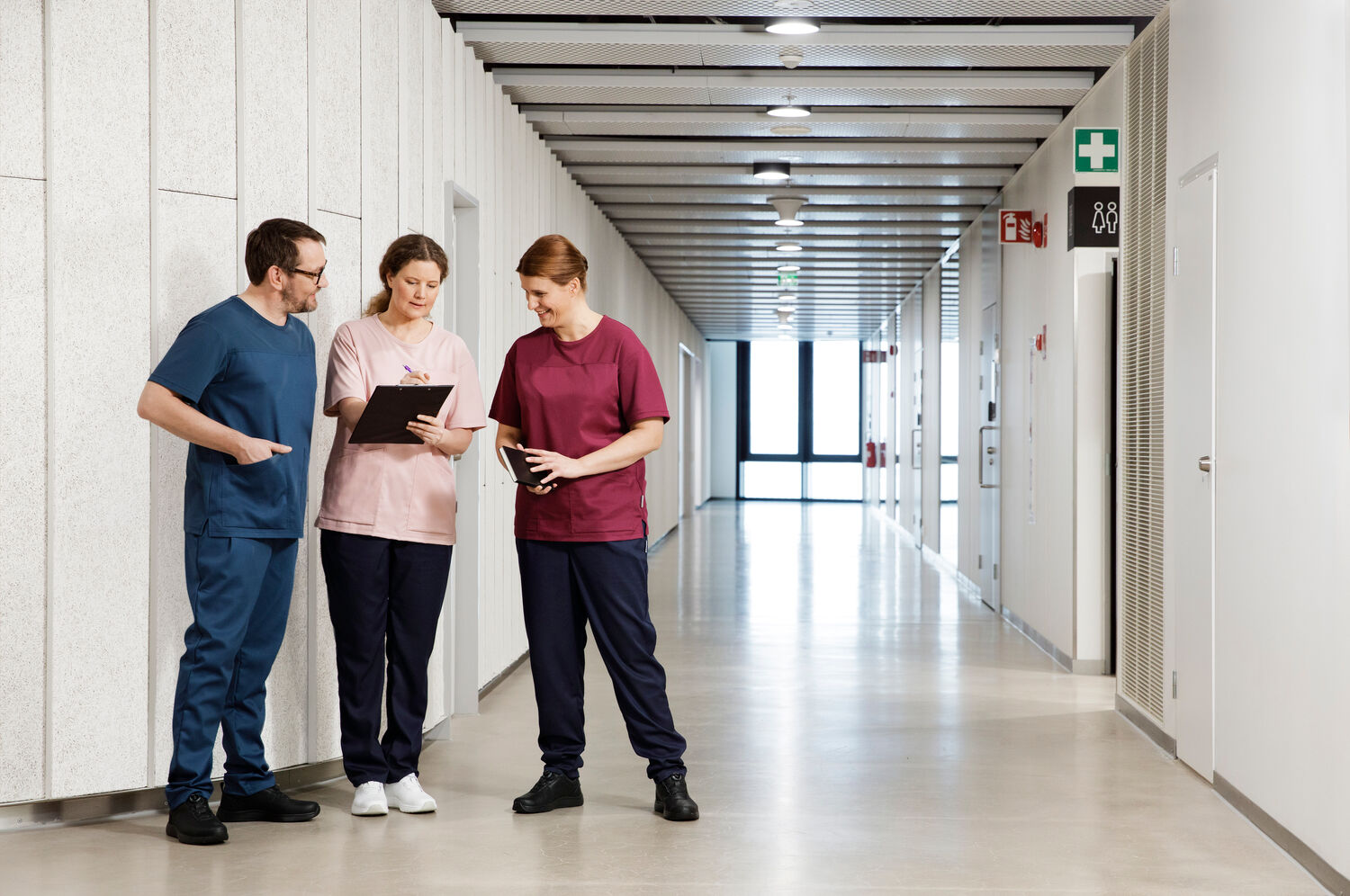
Towards sustainable workwear – together
What makes workwear sustainable? For Carrington Textiles, it’s about understanding and reducing the environmental impact of the garment throughout its entire life cycle.
“In the 1940s and 1950s, the river in the back of the factory was running a different colour. Thankfully, the business today is unbelievably different from what it used to be”, notes Jonathan McKendry, Export Sales & Marketing Manager at Carrington Textiles.
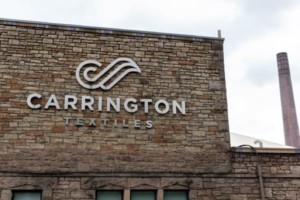
Carrington Textiles, the UK’s largest workwear fabric manufacturer and a long-time partner of Lindström, has its roots in Manchester, once the centre of the global textile industry. A lot has changed since the heyday of the “Cottonopolis”, one of the biggest shifts being in the attitudes towards the environment.
“Understanding of the environmental impacts of the business has grown massively over the decades. Also, the demand for sustainable products has skyrocketed in recent years,” explains Carrington Textiles’ Research and Development Manager Kristy White.
“In the past, the main concern about workwear was the cost. Now there’s a real push into redesigning the product to make it more sustainable.”
Carrington Textiles manufactures over half of all the fabric Lindström uses annually, roughly 2 million metres, the majority of which comes from the Carrington Textiles’ factory in the UK. One of the reasons why Lindström chose Carrington Textiles as its main fabric supplier was the company’s ambitious attitude towards R&D and sustainability.
One fibre will not solve everything
But what is sustainability when it comes to workwear? For Carrington Textiles, it’s about understanding and reducing the environmental impact of the garment throughout its entire life cycle.
“We want to make sure that we’re producing an ethically sourced fabric that is sustainable in terms of longevity and colour fastness, and that has the least environmental impact throughout its production,” explains McKendry.
Carrington Textiles International produces about 130 million metres of fabric each year in its factories around the world. Since 2019, the facilities have been following the ISO 50001 energy management standard. Energy consumption is tracked in real-time and excess energy and heat are utilised as much as possible throughout the process.
Sustainability is also an integral part of product development. Carrington Textiles’ R&D department is currently working on 80 different kinds of products, all of which have sustainability woven into them.
White explains that there is no one single fibre that will be the final answer to the sustainability question:
“A fibre that is more sustainable in one way can have some other kind of negative impact on the environment.
We need to take that into consideration.”
For example, extracting fibre from bamboo requires a lot of chemicals. Producing some fabrics demands less water, but their colour retention or durability is not sufficient for workwear that is worn and washed countless times.
The effort of producing sustainable fabric goes to waste if the garment doesn’t serve its purpose. Therefore, collaboration is key when deciding whether a new fabric meets all the requirements.
“We have just kicked off a collaboration with Lindström using our regenerative cellulose fibre. The fabric will be sent to Lindström for field testing and validation to make sure we have a sustainable product,” White explains.
What to do with worn workwear
While workwear is usually worn a lot more than average high street fashion, it too reaches the end of its life sooner or later. Both McKendry and White emphasise that one of the biggest challenges the textile industry faces is deciding what to do with all the discarded clothes. Instead of ending up in a landfill, the textiles can be reused in other products, such as a mattress or car seat fillings, or the fibres can be recycled into new fibres for clothing.
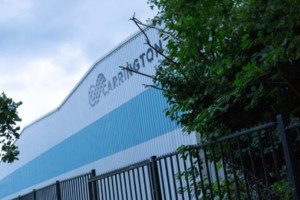
Designing and manufacturing workwear means balancing functionality, safety, and sustainability. McKendry explains that the different important functionalities, like zippers, or essential safety features, such as reflective parts, can make the garment more difficult to reuse and recycle.
“This is something designers need to take into consideration. The workwear looks beautiful and it’s practical, but it can’t be stripped apart as easily.”
Recycling the fibres is another challenge. From the environment’s perspective, the ideal workwear is made of pure cotton or other mono-fibres that are easy to convert to new fibre. Most of the workwear, however, is made from functionally superior poly-blend fibres which are more difficult to recycle mechanically or chemically.
Solving the problem of worn workwear requires collaboration throughout the value chain. While the textile industry is continuously discovering new ways to recycle garments, the infrastructure needs to process a much bigger flow of textiles.
“Making sure we are having the least environmental impact requires a holistic view,” White sums up. “You cannot have tunnel vision.”
About Carrington Textiles:
- The UK’s largest workwear fabric manufacturer, celebrating its 130th birthday this year.
- Production capacity of 55 million metres in 2020, exporting to 80 countries. Production facilities in the UK, Portugal, Russia, and Pakistan.
- Fabrics are Öko-Tex Certified.
- The main production facility, Pincroft Dyeing & Printing Co. Ltd, is in line with the ISO 140001 certification and operates one of the largest heat recovery systems of its kind, reducing CO2 emissions by 4,000 tonnes, annually.