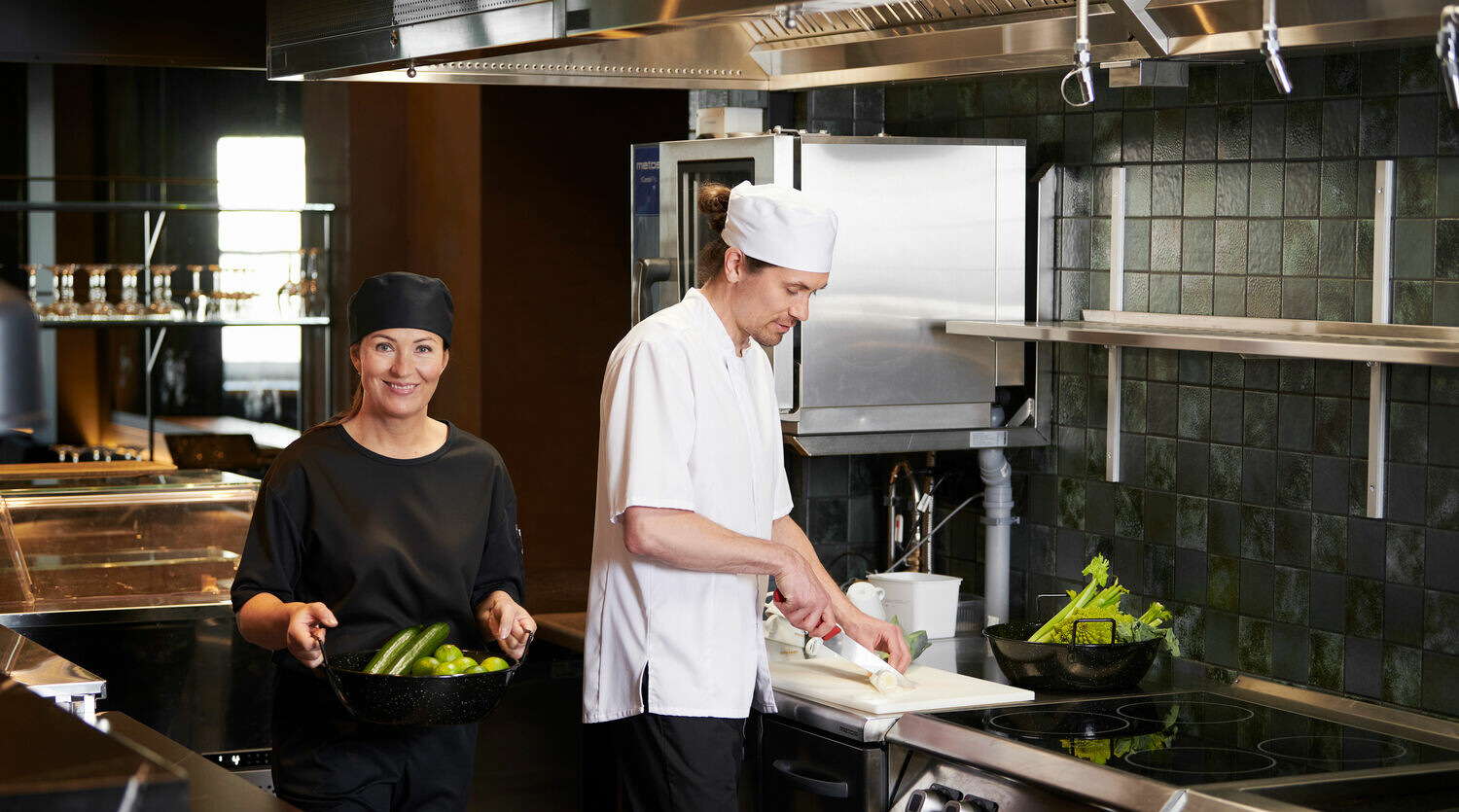
Our HoReCa workwear collection meets climate challenges
When we consider our ambitious climate targets, 25 percent of these reductions must be sourced from the footprint of textiles. Many readers and customers might not realise just how ambitious these targets are within the context of complex textile processes. In this article, we interview Elina Harjanne, Senior Manager of our workwear collections and Soile Pakarinen, Designer of our HoReCa garments to find out what achieving these objectives truly means and how they are meeting the challenges head-on.
The road to a more sustainable industry
Despite some companies pursuing a progressive sustainability agenda, the textile industry as a whole is lagging behind. “When I started in the industry, it was all about ‘fast fashion’. The accepted norm was to create collection after collection as quickly as possible, with little to no regard for the waste involved,” explains Pakarinen.
Worldwide, the textile industry is estimated to be responsible for around 10 percent of annual global carbon emissions, and that figure is only expected to increase significantly over the coming years. The increasing sustainability of collections produced by Pakarinen and Harjanne, along with the company’s work in general, will impact the ecological footprint of our value chain and hopefully have a knock-on effect on the wider industry.
Aiming for transparency in the entire value chain
One of the greatest difficulties is obtaining data to evaluate the true performance in reducing emissions. “From the cotton field to delivery, it’s a real challenge to get complete data sets from across the value chain. The whole industry has only relatively recently been waking up to the issue,” highlights Harjanne.
Despite this lack of data, it’s important to note that Harjanne and the team have been working with partners like Carrington to move in the right direction. ”There are many players in the textile production chain, which is why we work closely with fabric manufacturers. Open communication is the key to transparent supply chains in the future,” outlines Harjanne.
The key to success is making it last
The key word here is durability if we look at how sustainability has influenced the design process. The overwhelming message to customers from Harjanne and the team is, “Don’t sacrifice durability!” “Even if the emissions are higher for a product using more virgin fibres, its longer life-cycle can mean it’s far more sustainable.” As well as emissions, we are also considering the broader ecological impact, like the intensive use of land and water in cotton production, for example.
Within the design process of the HoReCa workwear collection, sustainability was considered in a variety of ways. Firstly, the team has a lot of experience co-creating for emotional durability with clients like S-Group. This long-term thinking involves engaging in a more collaborative relationship with the client and their staff, to help them change mindsets and attitudes towards clothing.
“A nice and unforeseen example of the attachment people can develop for clothing how staff at one company competed for the most used and softest garments when we returned them from the laundry. This totally surprised us,” laughs Pakarinen.
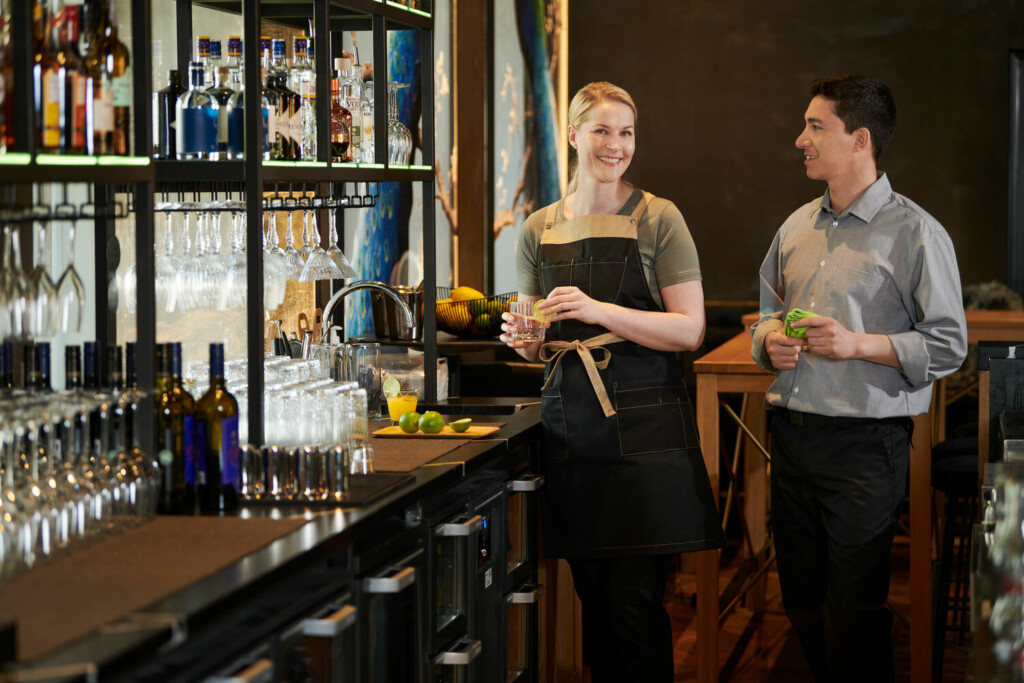
Designed for durability
Like other collections, the HoReCa workwear needs to be durable enough to withstand robust cleaning and the demanding physical work they are used for. “For sectors like food and healthcare, it’s important that our laundry service follows the EU standard EN-14065 to ensure the required hygiene level throughout the service process. This means garments must be more durable and sustainable,” explains Harjanne, before emphasising how “durability is not something with which we can compromise.”
The demanding maintenance process means fibres have a longer shelf-life than alternatives. Our maintenance service includes clothing repair, which influences style, as garments are fitted with adjustable features or reinforced with patches in areas that receive a lot of stress.
One example that particularly stands out is the minimal waste apron. Pakarinen and the design team found ways to optimise the use of fabric by minimising the amount of cutting waste in production. “We calculated that we were able to use an average of 92%, and as much as 97% for some pieces of fabric,” enthuses Pakarinen. The HoReCa garments are standardised so that the repair process is incorporated at the design stage. Easily repairable features are indicative of our collections as we seek ways to keep our garments in use for longer.
In the textile industry in general, approximately 15 to 20% of the bought fabric is lost in the garment cutting process and is landfilled, incinerated, reused, or recycled. Possibilities to reduce fabric waste must be found in the garment designing and development process. This also has a significant impact on revenue generation in the long term.
Tools for a more sustainable future
The HoReCa workwear collection is the first entire collection to utilise recycled materials. In particular, it is an example of ‘closed-loop’ recycling. “As well as repurposing all sorts of other recyclables, like plastic bottles, for example, we have also been able to incorporate recycled fibres from our old clothing as raw material for new garments,” states Harjanne.
The closed-loop process takes end-of-life garments which are first separated by the laundry department. Once these have been recycled into new fibres, they are then made into new material by our fabric producers.
The Senior Manager is quick to qualify, however, because durability is the priority; at the moment closed-loop materials only represent 10 percent of finished fabric in use. However, various recycling technologies are developing enormously, and Harjanne is hopeful that more closed-loop materials can be incorporated in the future.
In addition, Pakarinen is excited about the potential that 3D technology could bring to the design process, especially in reducing the waste of materials in the testing stage and on the cutting floor. Of course, the use of this technology is still some time away, but it is another example of how we can move the dial even further towards a more sustainable future.
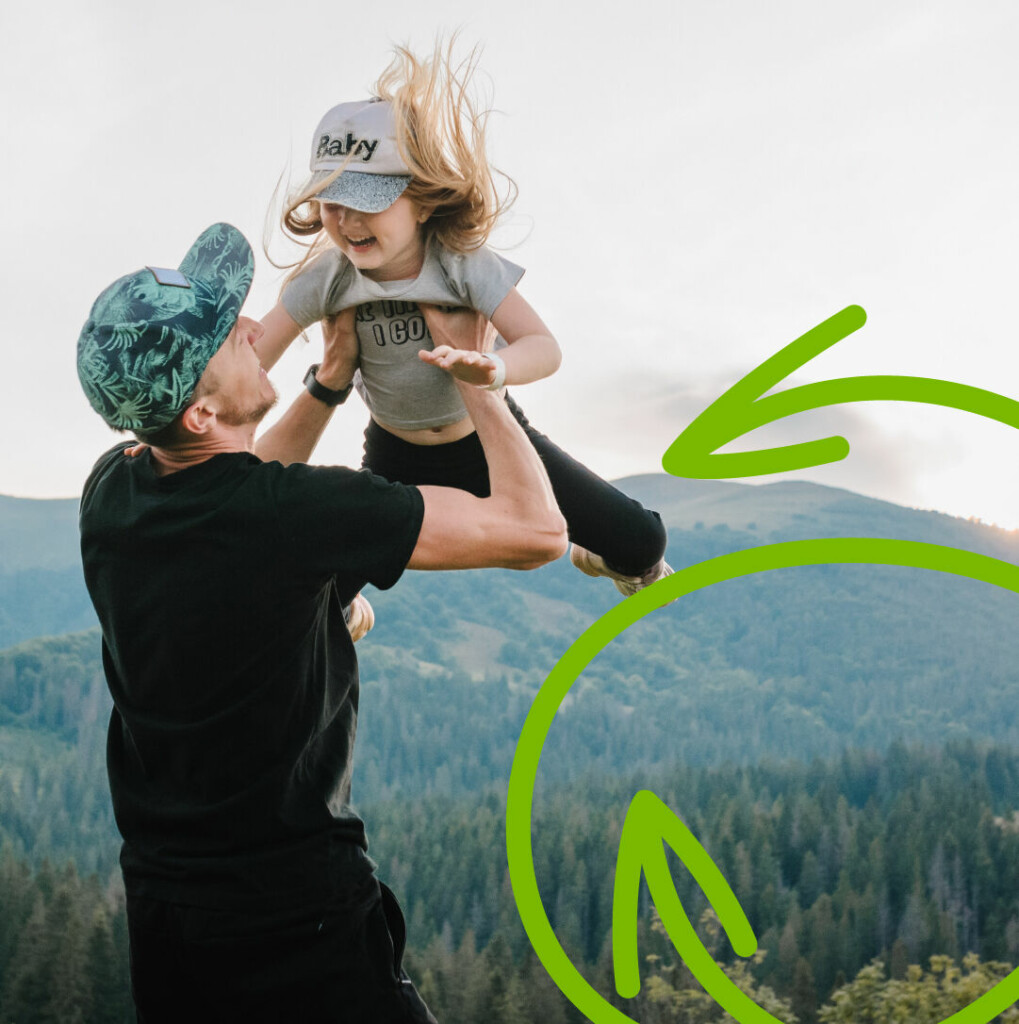