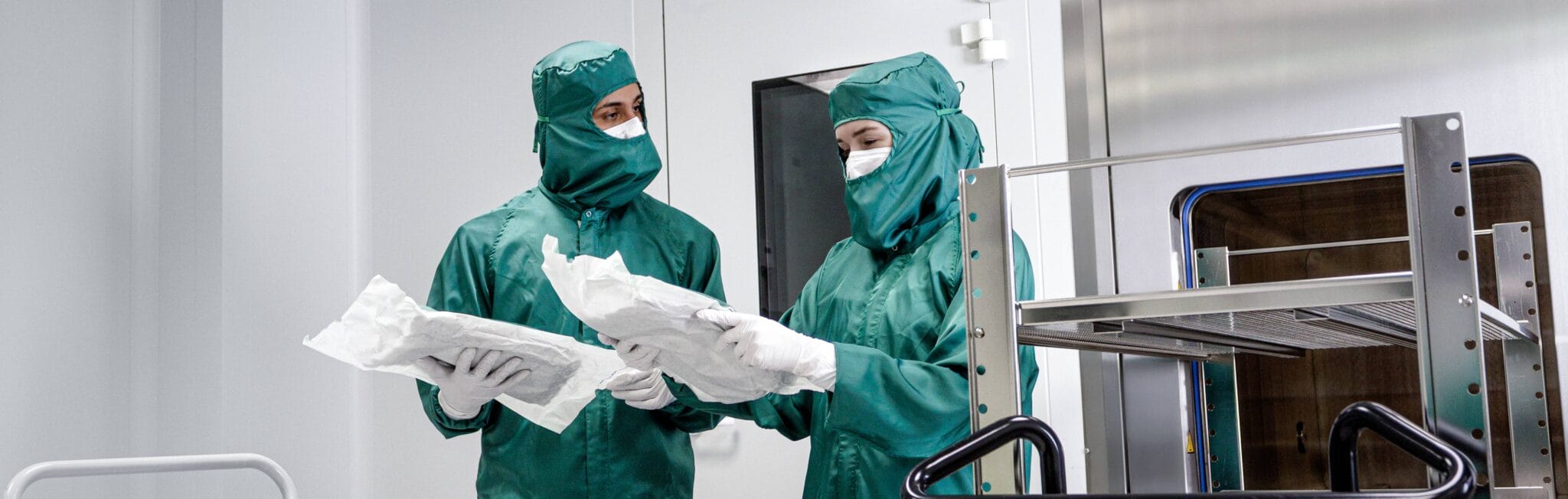
Contamination control is key in Good Manufacturing Practices
The biggest challenge in any cleanroom environment is preventing contamination – whether it comes from humans, processes, or materials. Garments play a crucial role in contamination control, and adhering to Good Manufacturing Practices (GMP) is essential for maintaining a sterile production environment. Lindström provides innovative solutions to help pharmaceutical companies meet GMP requirements efficiently.
Good Manufacturing Practices (GMP) are quality assurance standards ensuring that pharmaceutical products are consistently produced and controlled according to the required quality standards. GMP outline essential measures for both production and quality control, ensuring that processes are defined, validated, reviewed, and documented.
GMP also covers the suitability of personnel, premises, and materials for manufacturing pharmaceuticals, biologicals, and vaccines. GMP guidelines for garments are not explicitly defined, but they follow the same principles as those set for controlled cleanroom areas.
Cleanroom garments must be carefully managed to prevent contamination. Over time, textiles deteriorate and may release particles, posing a risk to product safety. RFID technology helps track the garment lifecycle, ensuring that garments are removed from circulation after reaching their maximum washes. The selection and use of appropriate clothing are essential for maintaining a sterile environment and preventing contamination in cleanroom environments – particularly those regulated by Good Manufacturing Practices.
Ensuring GMP compliance with ease
The pharmaceutical industry is continuously under a scanner. Auditors and inspectors ask questions and demand extensive documentation. You must ensure adhering to the GMP standards – not once, not twice, but every time.
Manas Kumar, Global Director of Pharma at Lindström.
While the pharmaceutical industry is aware of and familiar with GMP requirements, audit processes can vary based on interpretations, market demands, and regulatory bodies. Different auditors may focus on different aspects, leading to inconsistencies that may be challenging for manufacturers. Companies are keen to understand audit findings, regulatory changes, and emerging technologies, such as lifecycle tracking for garments, to stay compliant and improve practices.
Lindström can help make your processes GMP compliant and reduce the burden of the documentation. We make it easy for you to access and share documents with auditors at the click of a button, helping you close audits quickly and efficiently. Instead of spending time searching for records, you can instantly retrieve details like when a garment was washed and sent. This is a huge relief for an industry already under pressure to maintain compliance, making the entire process smoother and more stress-free.
Keeping up with continuously evolving guidelines
Guidelines, practices, test processes, and requirements change, and you need to keep up with them. Good Manufacturing Practices are continuously evolving and regularly updated at both national and global levels to ensure the highest standards in manufacturing, particularly in contamination control. “What is considered good practice today may not be sufficient tomorrow”, Manas Kumar sums up.
Organizations follow the latest standards, such as setting limits on bacterial contamination in garments to prevent risks. Compliance is verified through audits, risk management, and routine checks to ensure garments remain free of bio load after washing, preventing contamination of the end product. This structured approach helps maintain quality and safety in manufacturing.
Lindström’s strength lies in our deep knowledge of GMP practices, process-driven approach, and reliability. We have designed our processes to consistently meet GMP standards, ensuring compliance not just once, but every time. With extensive industry experience, we bring unmatched expertise in handling GMP requirements, making us a trusted and dependable partner in the market.
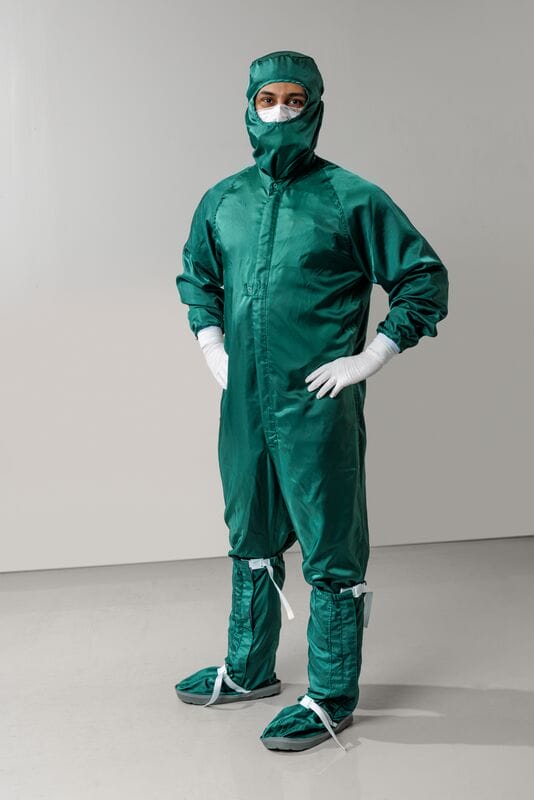
New testing methods for enhanced contamination control
Recent developments in GMP focus on improved contamination control, garment testing, and segregation of clean and unclean areas.
Validation has become an important point: how do you validate that my garment will last that long, and what are the test processes that determine how many washes the garment can take.
Manas Kumar, Global Director of Pharma at Lindström
New tests, such as the body box test (particle containment test), assess how well garments prevent contamination over time, ensuring they act as an effective barrier in sterile pharmaceutical industry environments. Life cycle validation is also becoming crucial to determine when garments should be replaced.
Additionally, new updates in guidelines emphasize stricter laundry practices to prevent recontamination. The use of barrier washers – machines with separate clean and unclean sides – is now recommended to eliminate cross-contamination risks. Regulatory bodies worldwide are adopting these guidelines, and companies are closely monitoring audits to understand how these changes are being enforced.
Key takeaways
Interpreting GMP guidelines and applying them in real-world cleanroom garment practices is essential for ensuring compliance and contamination control. Regulators require thorough testing and validation of garments, fabrics, trims, and stitched products to meet industry standards. On the laundry side, maintaining validated washing cycles and strict segregation between clean and unclean garments is critical to preventing cross-contamination. These practices, outlined in Annex 1 of the EU GMP, serve as a foundation for maintaining cleanroom integrity.
Lindström emphasizes key values to support pharmaceutical manufacturers in their GMP adherence, ensuring compliance with industry regulations by offering reliable, sustainable, and cost-effective solutions. In addition to providing high-quality garments and laundry services, Lindström actively helps clients navigate regulatory requirements, ensuring their cleanroom operations remain compliant, efficient, and environmentally responsible.
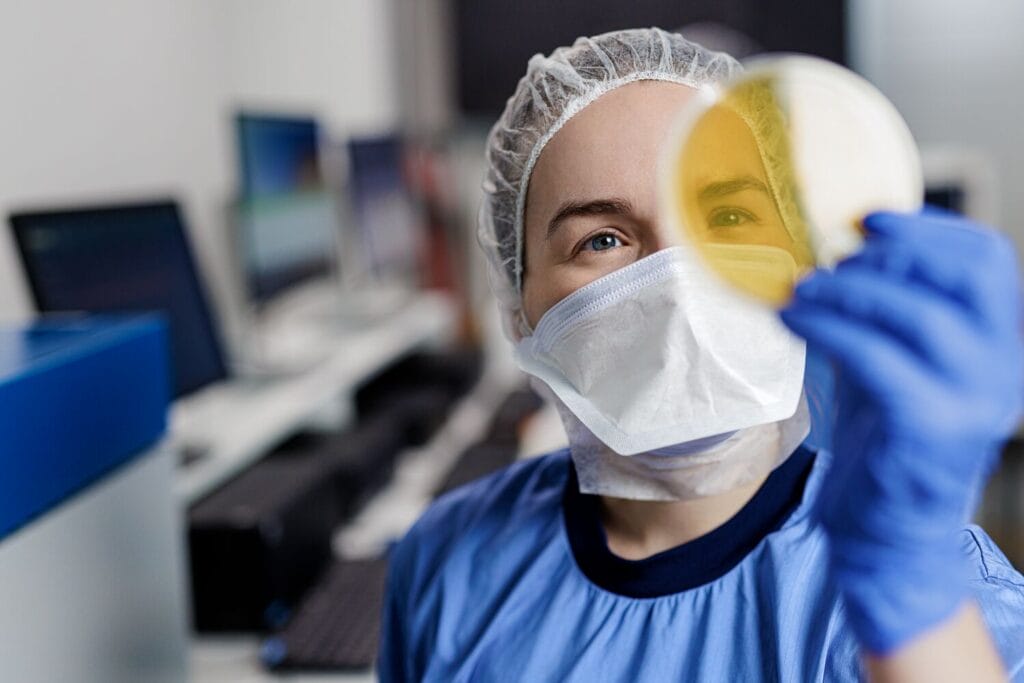