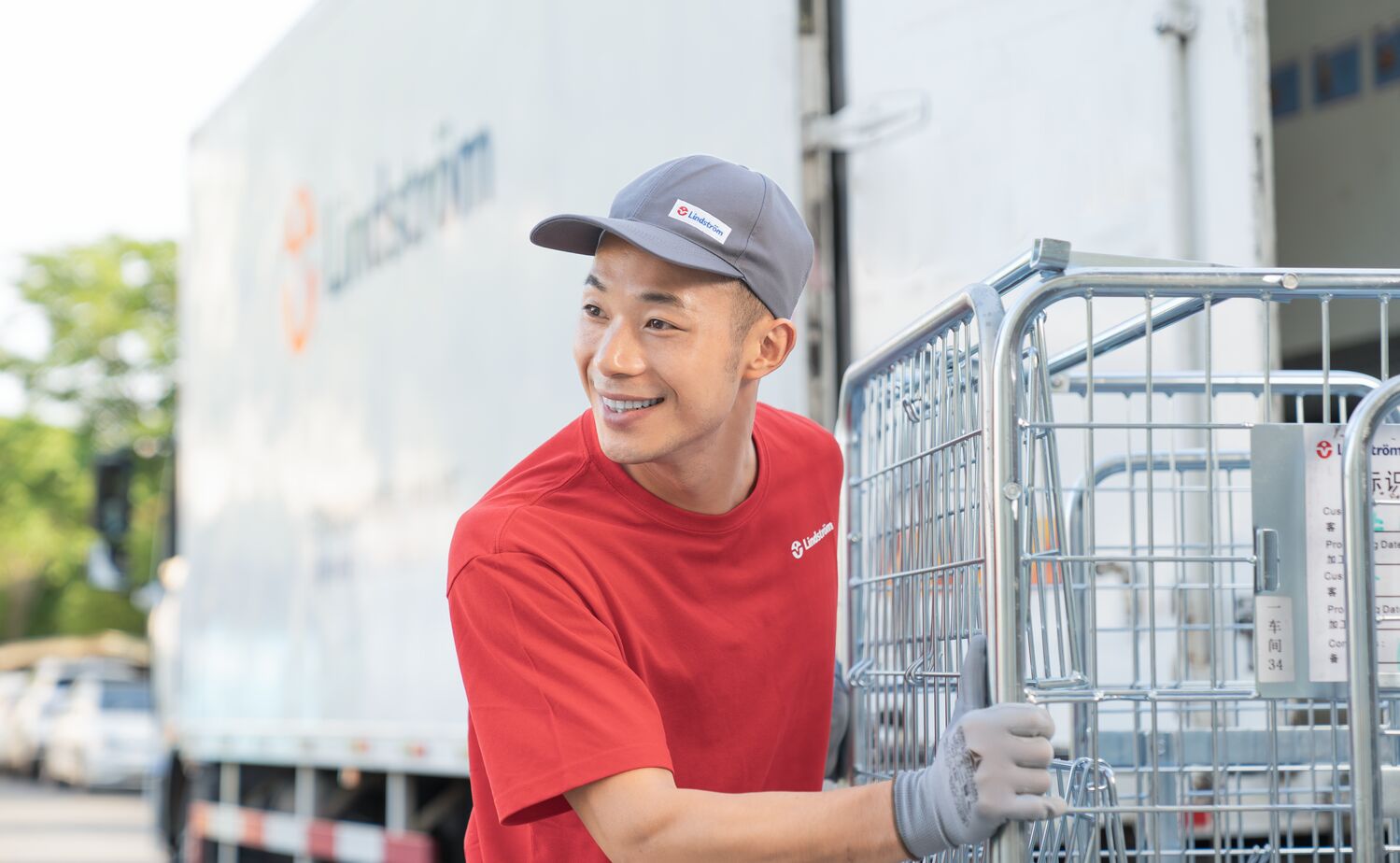
Strategic solutions for workwear procurement
Picture yourself as the person in charge of buying garments and textiles for a company. You have taken it upon yourself to handle this task, thinking it would be cost-effective and manageable. But soon, you find yourself overwhelmed by the variety of garments and the strict industry regulations you must follow. You start to wonder if there is an easier and more effective way to handle workwear procurement. Finding the best workwear management solution, you soon realise, needs to become a top priority.
Workwear procurement challenges
Every role at your company requires specific workwear. If you are in charge of buying work clothes for a restaurant chain, for example, you are not just getting uniforms for hosts and wait staff; you are also responsible for outfitting the chefs, kitchen staff and other employees. You have to think about the garments each person needs and make sure everyone has the right size. It can be tricky and take up a lot of time. If you are doing the buying yourself, it might also mean spending a lot of money upfront.
Furthermore, as you try to adapt to changing circumstances, such as employee turnover and evolving regulations, you might end up making many small-volume purchases – and at irregular intervals. These small-volume purchases not only drive up costs but lead to unpredictability in prices. Moreover, the lengthy lead times, especially for customised garments, add to your challenges. To ensure availability, you may end up overstocking garments, further increasing costs.
All the time you spend on workwear procurement takes away from doing other important things. It is not just about money; it is also about how much time and effort you have to put in. Making sure all your workwear is clean and safe leaves you with less time to focus on other tasks.
Meeting workwear challenges through Lindström’s solution
Thankfully, there is help at hand. We understand the challenges you face and have developed our workwear procurement solution to help you overcome these challenges. Here is how:
We handle things with speed and efficiency, so you can get back to focusing on your core tasks!
Purchasing workwear in a sustainable way
While we have touched on the environmental benefits of our solutions, it’s important to understand just how deeply sustainability guides our operations.
In today’s world, sustainability is not just a buzzword – it is a must. At Lindström, we design our solutions with sustainability at their core.
You have already seen how, by following circular economy principles, we minimise overproduction and textile waste in our operations. It is not just because we produce garments on demand, thereby avoiding the need for you to order workwear that goes unused. We also actively try to extend the lifetime of all textiles and produce new ones only when needed. By repairing, recycling and reusing garments, we avoid millions of kilograms of unnecessary textile production.
Another way our solutions contribute to sustainability is by minimising transport mileage. Imagine that your company uses multiple suppliers. Or suppose your company has multiple facilities, and each manages its workwear procurement independently. It would mean increased carbon emissions from multiple vehicles travelling to and from different suppliers. It would also mean more packaging waste from individual deliveries. But we streamline this process for you. Textiles are manufactured in the closest production sites, and workwear is delivered with optimised loads and routes. This minimises the environmental impact associated with transportation.
For us, sustainability is not just a checkbox – it is a fundamental part of who we are and what we do.
The added value of using Lindström for workwear procurement
So what does this all mean for you? All sectors interested in purchasing workwear – whether it be the construction industry, healthcare or food manufacturing – will gain added value from our solution. The benefits of using our solutions are:
- Minimal upfront costs and a lower unit cost for each purchased garment
- On-demand customisation of garments delivered in a timely manner
- Efficient availability of new garments, thereby reducing your need to stock workwear
- Strict compliance with industry standards and regulations
- The lack of need for you to allocate workforce and resources for purchase processes
- A sustainable, environmentally–friendly solution that reduces emissions, garment overproduction and textile waste.
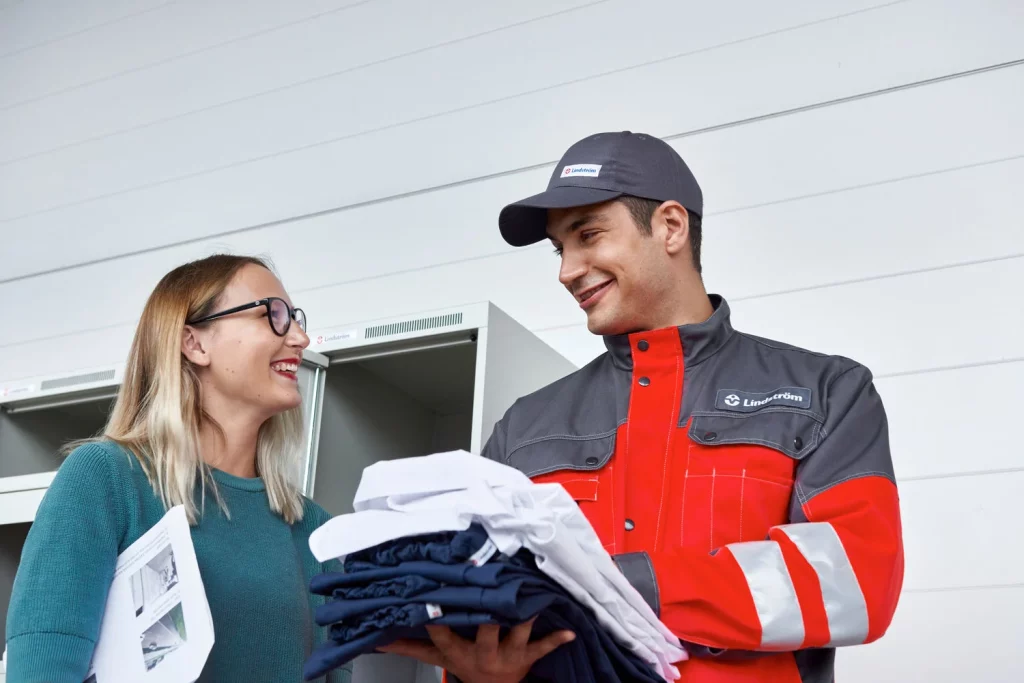