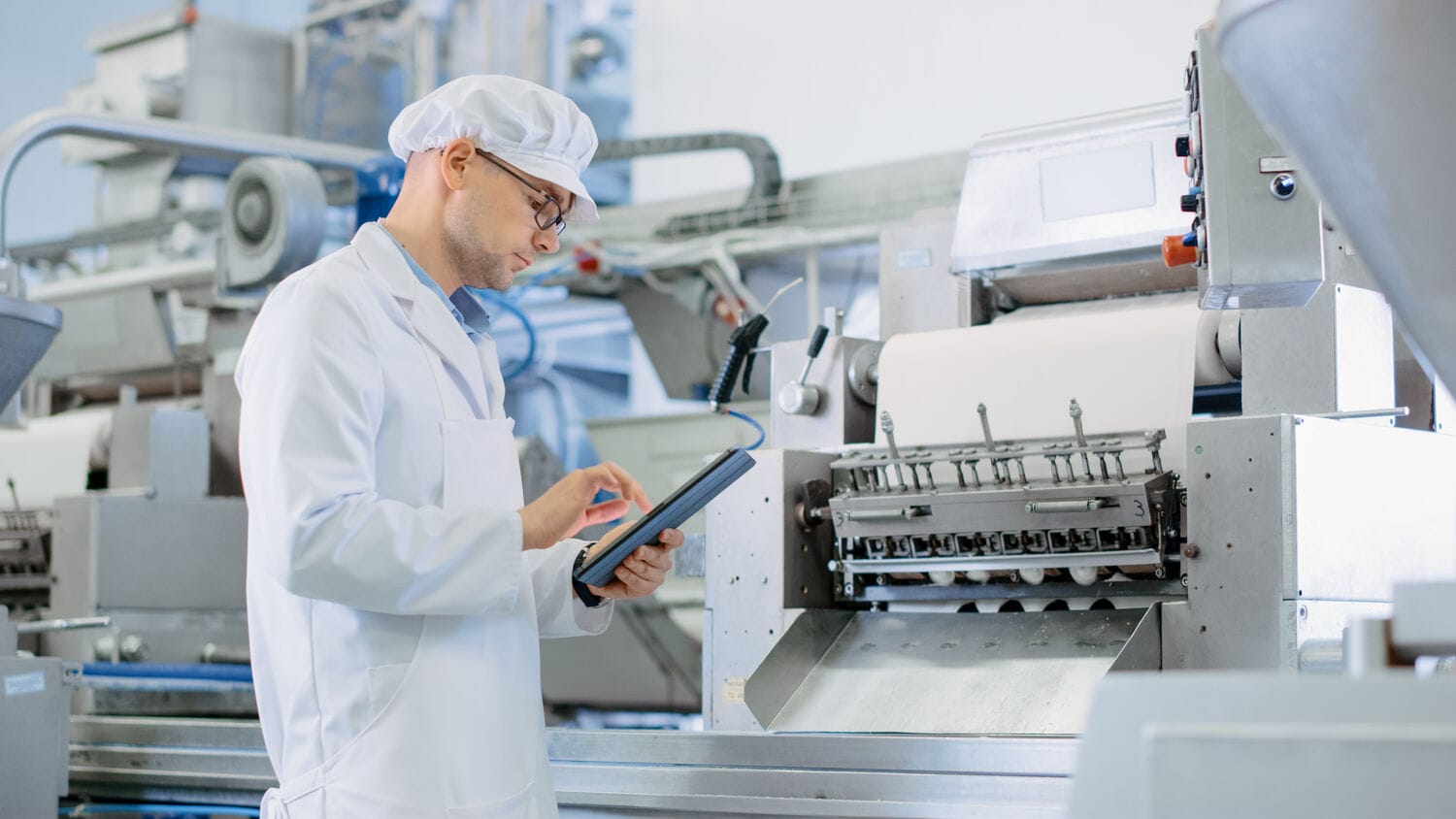
How to implement quality culture in food organisations
The requirements in food industry are constantly evolving. To attain or maintain international food safety certifications such as ISO 22000, FSSC 22000, BRCS Food Safety, IFS Food, and similar, companies must follow several guidelines and constantly monitor upcoming changes. All the above standards and schemes expect food organisations to develop a food safety culture.
What exactly is a food safety culture? It is not just a buzzword! Companies should demonstrate their food safety culture through top management commitment to documentation, plans, maintenance, and improvements across the entire organisation. These are just a few of the most important aspects, while a true food safety culture can be seen in everyday company actions.
In this article, Lindström’s head of Food and Retail, Csilla Kovács-Rahói, shares her view on why quality culture development might bring better value for an organization, rather than building purely a food safety culture. How can it be implemented, what are the benefits to gain, and the risks to look out for?
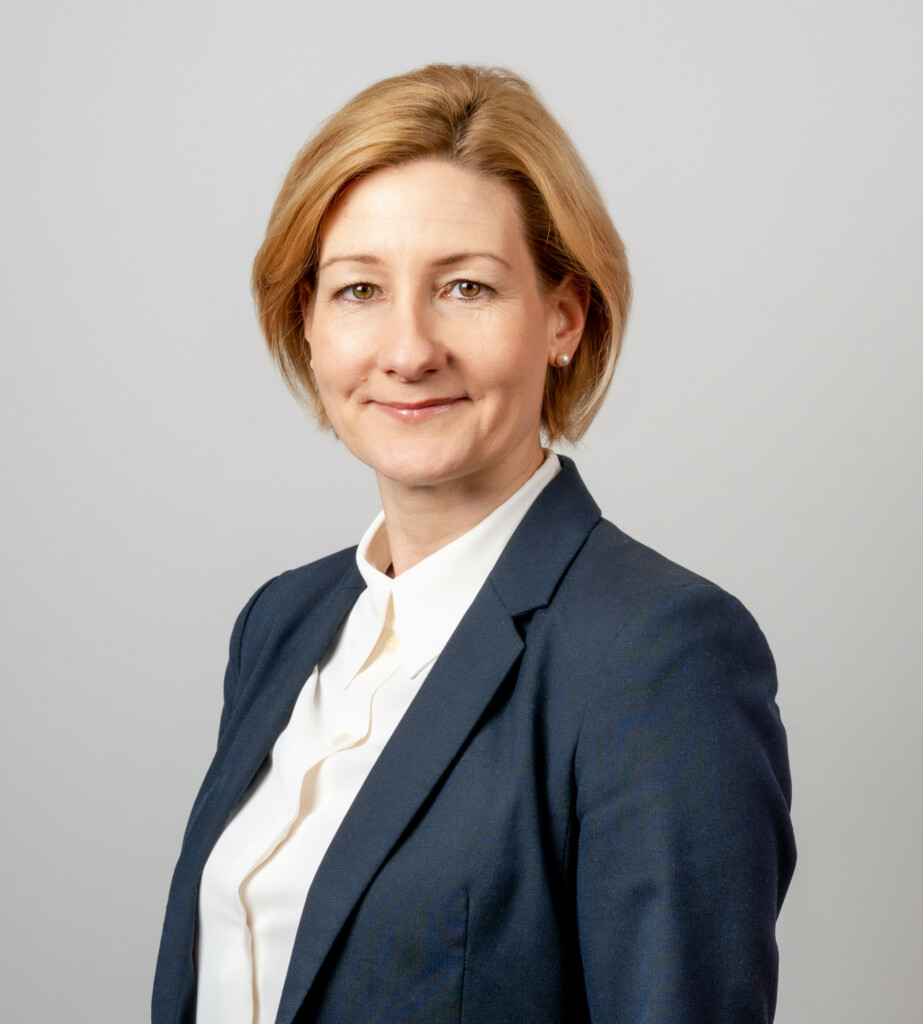
Why do we use the phrase “quality culture”, rather than “food safety culture”?
People sometimes perceive the term “food safety culture” as highly scientific or as the sole responsibility of the quality team. For instance, a logistic manager or procurement officer might think that food safety isn’t their direct concern. That is not true. The true meaning of ‘quality’ is that each employee pays attention to details, making sure their job is done well and according to the defined processes. When employees follow a quality mindset, it will result in improved food safety.
In logistics, for example, you must design processes with quality in mind, ensuring labels are accurate with clear nutrient and allergen information, proper product delivery, and so on. The goal of everyone in the organisation should be to produce high-quality food, with every department playing a role in achieving this. Hence, the term quality culture is more relatable across departments than food safety culture.
When an organization commits to establishing a quality culture, it must consider local cultural factors, including educational and economic contexts.
Quality culture can be established for one organisation, but also for larger entities like companies with multiple subsidiaries in different countries. While cultures can be vastly different, they often also connect with each other on a deeper level. It goes deep into our heart, and we might need to find different paths to reach everybody with it. Each individual should be able to interpret the quality culture and feel that they are working in the right way and following correct processes.
Csilla Kovács-Rahói, Head of Food Industry at Lindström Group
While we know theoretical aspects like leadership commitment, employee involvement, continuous improvement, recognition and rewards, and training and development, the challenge is to implement these principles in practice successfully.
5 steps of implementing a quality culture
1. Leadership commitment
Effective leadership is about more than just making posters or public statements. True commitment means that each department head understands how to contribute to quality with their team. While the approach may vary between departments—be it logistics, marketing, or facility management—the core values remain the same. The desired processes should be clearly described, and everyone needs to be committed and involved. Leaders should act as a role model and lead by example.
2. Employee involvement
Everyone, from the janitor to the board of directors, should feel connected and contribute to fostering quality culture. Engaging people at a personal level is crucial. Getting to the heart of people happens through connecting. It can be related to the consumer group, to a tradition, or something else.
Csilla brings an example from her previous role, where they produced baby food. Nearly everyone has children or a relative with children. Everyone could relate to that, and their common goal became to produce safe food for them. That was something all could commit to, wanting to do the right thing and wanting to improve.
3. Continuous improvement
Developing a quality culture takes time—you cannot rush it. Expect it to take more than a month, and even a year—but it will pay you back significantly!
Continuous improvement begins with leadership and extends to every department and team member. Regular discussions and communication are essential for keeping quality culture alive, ultimately leading to it becoming a daily practice.
4. Recognition and rewards
Recognition is a powerful motivator. We are all human beings who want to feel valued for our contributions. When developing a reward program, ensure that it is consistent across all departments to promote equal engagement and positivity around quality culture. None of the departments roles should be over estimated above others.
5. Training and development
Training isn’t a responsibility that is only on the shoulders of the quality and compliance team. To truly cultivate a quality culture, department heads must actively train their teams, providing examples relevant to their specific functions. This personal approach ensures that everyone in the organization understands and implements quality standards.
Benefits of an active quality culture
Improved efficiency: When everyone understands their role in quality culture, compliance with processes improves, leading not only to increased efficiency but likely also fewer batch rejections and public recalls.
Improved compliance: Based on Csilla’s experience, implementing a quality culture can result in significant decreases in production failures, hence improve product(ion) quality. This can on average take up to three years’ time (dependent on the size of the organization and in case all above recommendations are followed). This saves money and product recalls will not cause your brand reputation to suffer.
Enhanced employee loyalty: A motivated and recognized workforce is more likely to stay, reducing HR costs and lowering employee turnover. Moreover, with fewer mistakes and less need for corrective and preventative actions, employees can focus on innovation. Allocating more time to that further strengthens the company’s reputation and competitiveness.
What are the risks in developing a quality culture?
Involving external suppliers and key partners
Once you establish a strong internal quality culture, it’s important to involve suppliers and key partners. Identify key suppliers from a food safety or business continuity perspective and set clear targets and KPIs for them. Building trust and creating educational opportunities around the quality program are key. Consider including quality culture as part of your supplier audit program to ensure they align properly.
Key takeaways
- Good work takes time – Celebrate each step in the journey.
- Consistency and commitment – Involve everyone, from leadership to frontline employees.
- Consistent messaging – Align everyone with the key message and purpose.
- Start internally and expand the quality culture to external suppliers and partners.
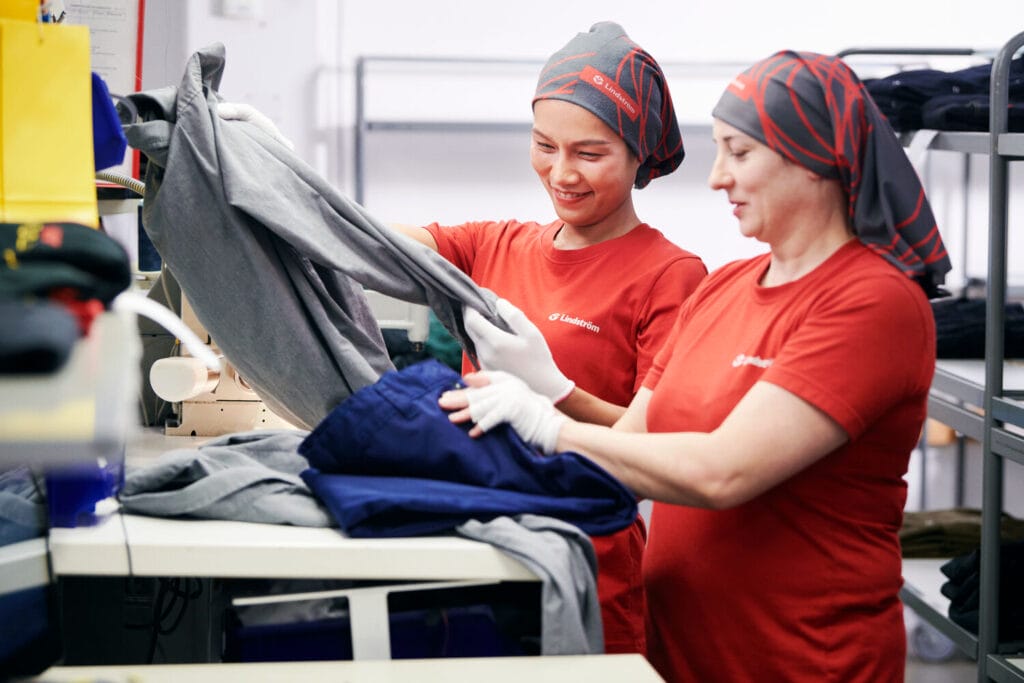